Introduction to Jet Pumps
Jet pump are unsung heroes in the world of industrial operations, quietly powering processes that drive productivity and efficiency. These innovative devices may not often steal the spotlight, but their impact is profound. From water supply systems to chemical processing plants, jet pumps play a critical role in various applications, helping industries optimize performance while minimizing energy costs.
As manufacturing demands evolve and technology advances, understanding how jet pumps function and their advantages becomes crucial for businesses striving to stay competitive. This blog delves into the fascinating world of jet pumps exploring how they work, highlighting real-world success stories, addressing common misconceptions, and discussing future trends that could shape industrial performance even further. Buckle up as we dive deep into the mechanics behind this essential equipment!
How Jet Pumps Work
Jet pumps operate on a simple yet effective principle of fluid mechanics. They use high-velocity jets to create a low-pressure zone, drawing in the surrounding liquid. Essentially, they harness the power of kinetic energy.
A jet pump comprises two main components: the nozzle and the diffuser. The nozzle accelerates water through a narrow opening, turning it into a fast-moving stream. As this stream exits, it creates suction that pulls additional liquid from an external source.
The diffuser then converts this velocity back into pressure as the flow expands. This transformation enables efficient lifting and moving of fluids over varying distances without requiring complex machinery.
Jet pumps are versatile devices used across many industries due to their ability to handle solids and slurries with ease, making them suitable for challenging applications where other pumping solutions may struggle.
Advantages of Using Jet Pumps in Industrial Settings
Jet pumps offer several significant advantages in industrial settings that enhance operational efficiency. Their design allows for effective fluid handling without the need for complex mechanical parts, reducing maintenance costs.
Another benefit is their ability to handle a wide range of fluids, including corrosive and viscous materials. This versatility makes them ideal for various applications across industries, from chemical processing to mining.
Jet pumps also excel in providing high flow rates while maintaining low energy consumption. This efficiency not only lowers operating costs but also aligns with sustainability efforts as companies seek greener alternatives.
Moreover, they are relatively easy to install and can be integrated into existing systems with minimal disruption. This adaptability ensures that businesses can upgrade their operations swiftly.
Jet pumps require less space compared to traditional pumping solutions. Their compact size allows for more efficient use of available floor space within facilities.
Case Studies and Real-world Examples of Improved Performance with Jet Pumps
Several industries have witnessed remarkable improvements after incorporating jet pumps into their operations. For instance, a chemical manufacturing plant in Texas replaced its conventional pumping system with a jet pump solution. This switch led to a 30% increase in efficiency and reduced energy consumption significantly.
In the water treatment sector, a facility in California adopted jet pumps to enhance their filtration processes. The result was faster processing times and lower operational costs, allowing them to handle larger volumes without compromising quality.
Another example can be seen in the oil extraction industry. A company utilized jet pumps for enhanced oil recovery techniques, leading to higher yield rates from existing wells while minimizing environmental impact.
These case studies illustrate how versatile and effective jet pumps can be across various industrial landscapes. Their ability to improve performance is not just theoretical; it’s proven by real-world applications that deliver tangible results.
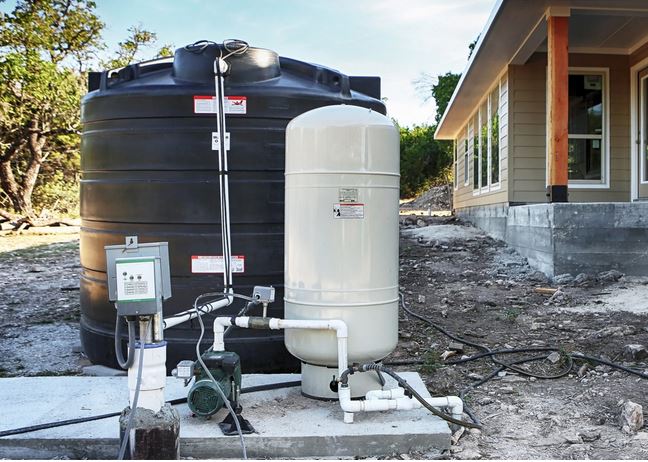
Common Misconceptions about Jet Pumps
Many people believe jet pumps are outdated technology. In reality, they have evolved significantly to meet modern industrial demands.
Another common misconception is that jet pumps cannot handle high-pressure applications. However, advancements in design and materials have made them highly efficient for various pressure ranges.
Some think jet pumps are difficult to maintain. On the contrary, their straightforward construction often simplifies maintenance tasks compared to other pumping systems.
There’s also a belief that they consume excessive energy. Yet, when properly sized and configured, jet pumps can operate efficiently while minimizing energy costs.
Many assume these pumps lack versatility. Jet pumps can actually be tailored for diverse applications from water supply to chemical processing, showcasing their adaptability in different industries.
Maintenance and Operational Considerations for Jet Pumps
Maintaining jet pumps requires attention to detail. Regular inspections can prevent costly downtime.
Proper operation is equally crucial. Operators should understand the pump’s specifications and limits. Running a pump outside its designed parameters can lead to inefficiencies or failures.
Fluid quality matters too; contaminants can damage components over time. Implementing filtration systems helps protect the investment.
Another key aspect is monitoring performance metrics like pressure and flow rates. Sudden changes often signal issues that need immediate attention.
Ensure all personnel receive training on safe handling practices and emergency procedures. Knowledgeable staff are vital in maintaining peak performance levels while safeguarding workplace safety.
The Future of Jet Pump Technology and its Potential Impact on Industrial Performance
The future of jet pump technology is promising, with advancements on the horizon. Innovations in materials and design are paving the way for increased efficiency and durability.
With industries focusing on sustainability, jet pumps can adapt to eco-friendly practices. This shift not only reduces energy consumption but also minimizes environmental impact.
Emerging smart technologies will enhance monitoring capabilities. Real-time data analytics may lead to improved decision-making processes for operators.
As automation becomes commonplace, integrating jet pumps into automated systems could optimize workflow significantly. Enhanced performance metrics can drive productivity like never before.
Additionally, research into alternative energy sources might revolutionize how these pumps operate. Flexible power options could make them more accessible across various sectors.
As we move forward, the evolution of jet pump technology holds significant potential to transform industrial operations dramatically.
Conclusion:
Jet pumps have carved a significant niche in the industrial landscape, offering solutions that enhance efficiency and performance. Their unique design allows them to handle various fluids effectively, making them suitable for diverse applications. As industries increasingly prioritize sustainability and cost-effectiveness, the versatility of jet pumps becomes even more critical.
Real-world examples demonstrate their capability to boost productivity while reducing operational costs. Many companies report improved output and lower energy consumption after implementing jet pump technology. These benefits highlight the potential of jet pumps in optimizing industrial processes.
Misconceptions about jet pumps often hinder their adoption. Understanding how they work and recognizing their advantages can help dispel these myths. Proper maintenance is essential as well; regular checks can ensure longevity and optimal performance.